In this blog we’ll clear the air on the differences between a consumer PC and an industrial computer. You’ll have the knowledge to specify the difference between the two, as well as, determine which is proper for your application. Understanding Industrial Computers: Key Features and Benefits for Your Business In today’s fast-paced, technology-driven world, industrial […]
Category: Industrial Computer
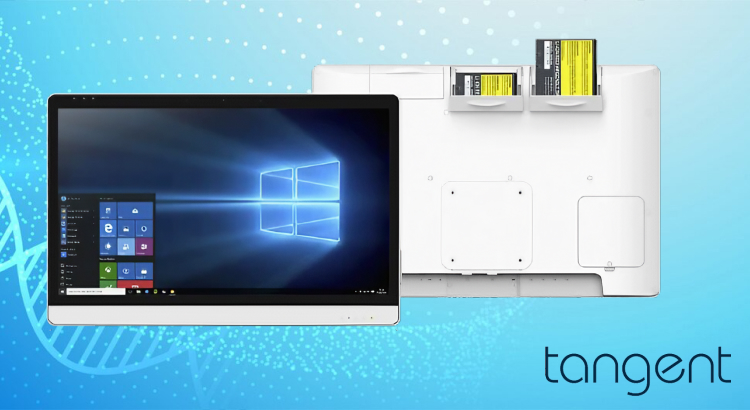
What is a Panel PC?
A Panel PC—an all-in-one computer integrated with a touchscreen—has emerged as a popular choice, offering unique advantages that cater to diverse applications, from industrial settings to healthcare facilities. This post will dive into what a Panel PC is, explore some of its key uses, and discuss why choosing a reliable provider like Tangent for your […]
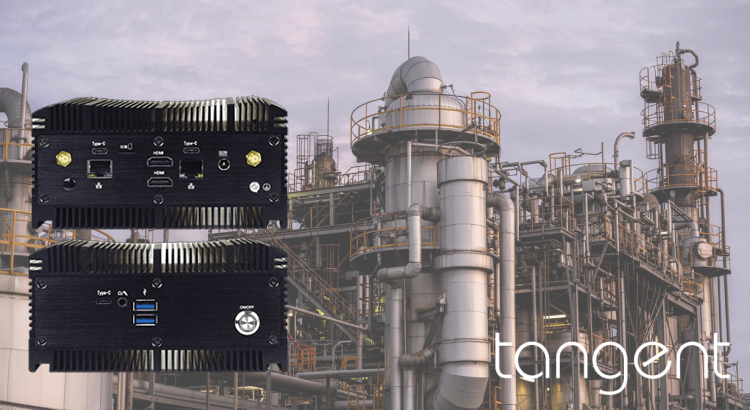
What Are the Best Rugged Mini PCs?
In industrial settings, such as, manufacturing and military settings, rugged mini PCs are essential for reliable performance in demanding environments. Unlike consumer-grade computers, rugged mini PCs are engineered to withstand extreme temperatures, shock, dust, and other harsh conditions, making them ideal for critical applications in factories, warehouses, field operations, and military deployments. Rugged mini PCs […]
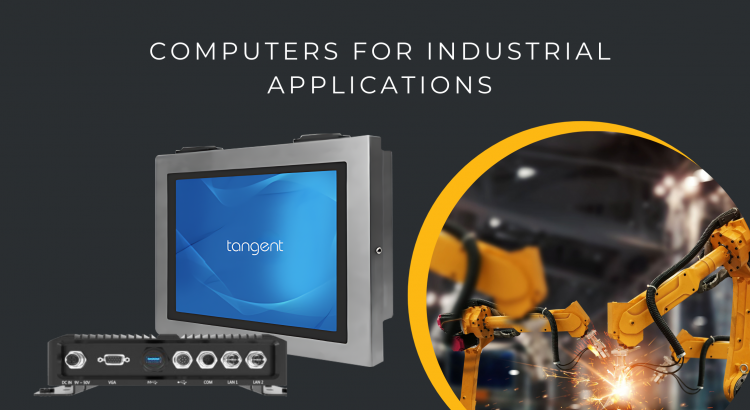
Which Type of Computer is Used in Industry?
Industrial Computers: Essential Solutions for Robust Applications The growing demand for robust computing solutions in various sectors has led to a significant reliance on industrial computers. These specialized systems are engineered for environments where typical consumer-grade PCs would falter. Industries ranging from manufacturing to construction find industrial computers indispensable due to their ability to withstand […]
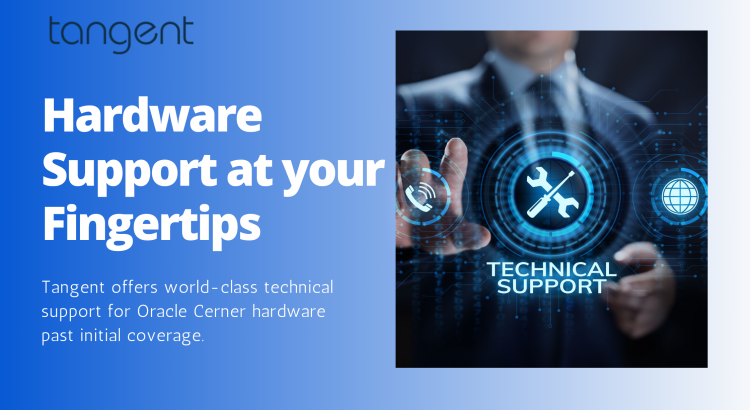
Hardware Technical Support from Tangent
At Tangent, we understand the frustration that comes with encountering hardware issues without the necessary support. Although you may be out of manufacturer coverage, your facility deserves dependable and trustworthy assistance. Our dedicated US-based support team delivers the highest standard of service you can rely on. Out of Warranty Coverage If you find yourself with […]
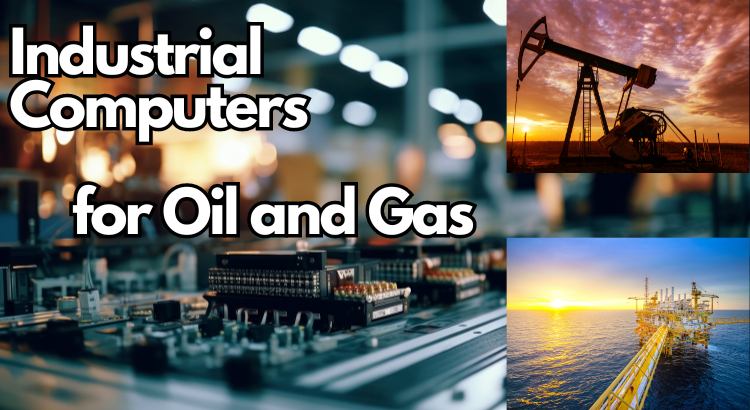
Industrial Computers Tailor-Made for Oil and Gas Sectors
Tangent’s explosion-proof computers are robust and purpose-built for the oil and gas industry. In environments characterized by the presence of flammable or explosive vapors or gases, such as those found in the oil and gas industry, prioritizing safety and reliability is of utmost importance. Tangent’s commitment of manufacturing best-practice purpose-built computers has heard the demands […]
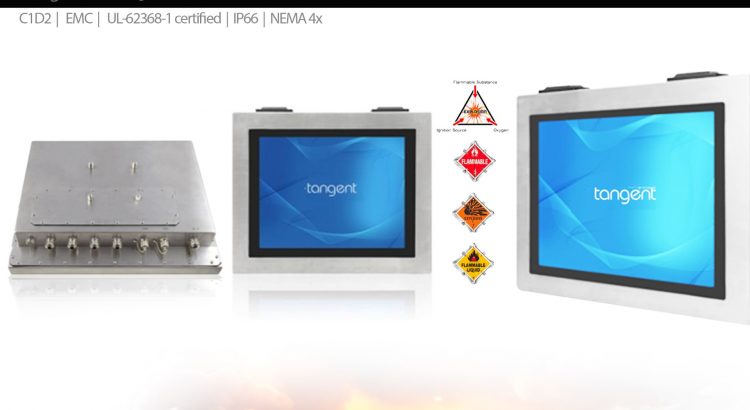
New Product Announcement: Industrial Explosion Proof VITA S C1D2 15″ and 22″ Computers
Tangent is thrilled to announce the release of its latest products, the Explosion Proof Panel PC, Vita S C1D1 15” and 22” series. Designed to meet the stringent requirements of hazardous environments, the Vita S Explosion Proof series computers have undergone rigorous testing to ensure safety, top performance, and offers the best solution for environments […]
How Industrial PCs are Revolutionizing Industrial Automation
Industrial automation has come a long way in recent years, and the rise of industrial PCs has played a significant role in this revolution. Industrial PCs are used to control and monitor a wide range of manufacturing processes, from assembly lines to robotic systems. In this blog, we will discuss how industrial PCs are revolutionizing industrial automation. […]
Choosing the Right Industrial PC for Your Manufacturing Needs
Manufacturing processes have become increasingly reliant on technology, and industrial PCs have become an essential component of these processes. However, selecting the right industrial PC for your manufacturing needs can be a daunting task. In this blog, we will discuss the factors you need to consider when choosing the right industrial PC for your manufacturing […]
Industrial PCs for Clean Room Applications
Clean rooms are critical environments used in industries like pharmaceuticals, biotech, and semiconductor manufacturing to maintain a controlled environment free of airborne contaminants. The stringent requirements for clean room environments make it necessary to use specialized equipment that can operate without causing contamination. Industrial PCs are an essential component in clean room applications, offering a […]