What Is a Touchscreen Panel PC & Where Is It Used? In today’s fast-paced world, where technology is constantly evolving, touchscreen devices have become almost second nature to us. From smartphones to ATMs, touchscreens are everywhere. But have you ever wondered about touchscreen panel PCs? These versatile devices blend the functionality of a traditional PC […]
Category: Industrial Computers
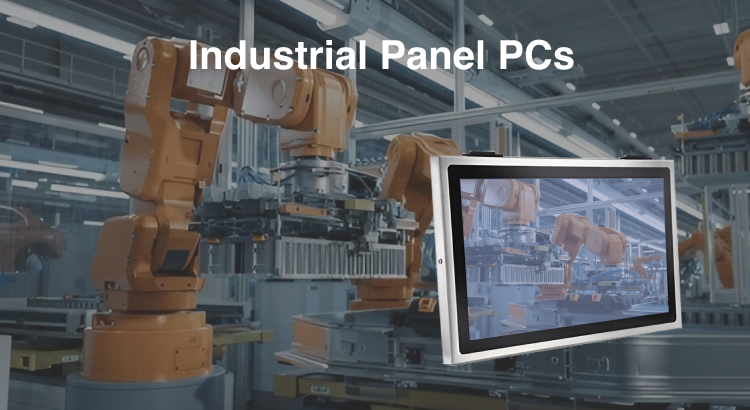
Industrial Panel PCs
Industrial Panel PCs are indispensable tools designed to tackle the most challenging automation problems. These robust systems are not your typical consumer-grade computers; they are built to withstand harsh environments and provide reliable, long-term operation. Our Panel PCs, in particular, offer a versatile and powerful solution for a variety of industries. Equipped with the latest […]
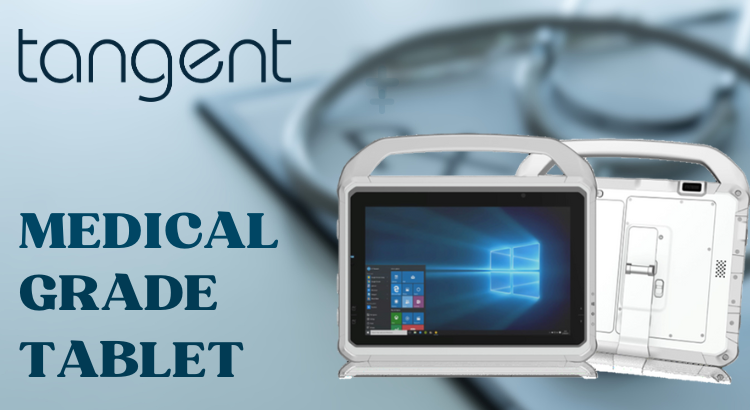
Medical Grade Tablet
In healthcare technology, the demand for reliable and robust devices is ever-growing. Medical professionals require tools that are not only efficient but also meet stringent regulatory standards. One such essential tool is the medical grade tablet. Designed specifically for healthcare environments, these devices offer a combination of durability, reliability, and compliance with medical standards. When […]
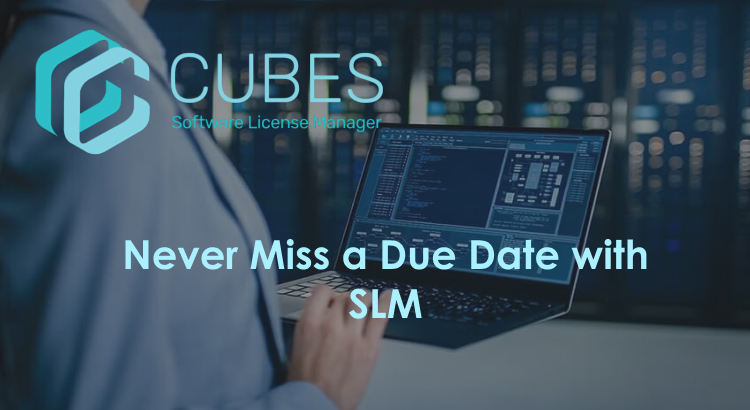
Never Miss a Due Date with Software License Management
Managing software licenses is a critical yet often overlooked aspect of IT operations. With the increasing reliance on various software solutions, keeping track of licenses, renewals, and compliance can quickly become overwhelming. Missing a due date for software license renewals can lead to costly consequences, including software downtime, compliance issues, and even legal penalties. However, […]
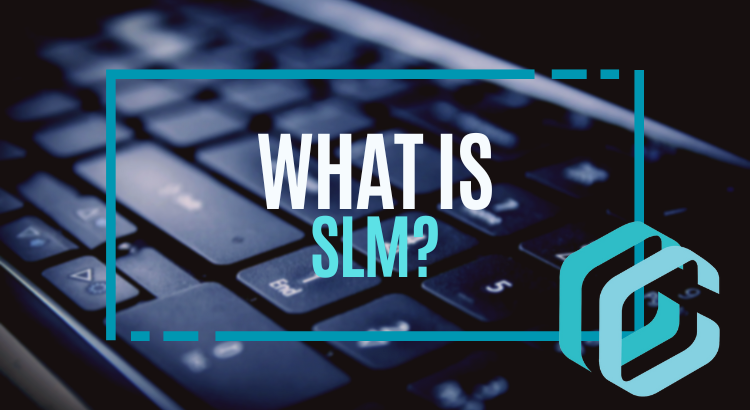
What is Software License Management?
Software licensing management is the practice of monitoring, documenting, and ensuring the proper use of software licenses within an organization. This process is crucial for both software vendors and users to ensure compliance, optimize software utilization, and avoid legal and financial penalties. Key Aspects of Software Licensing Management Types of Software Licenses Perpetual Licenses: Purchased […]
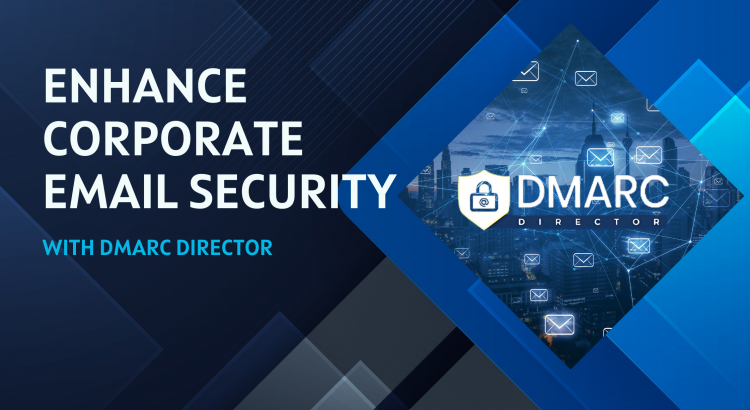
Prevent Corporate E-Mail Spoofing and Spam with DMARC Director
Email is a cornerstone of corporate communication, however, this essential tool is frequently targeted by cybercriminals through methods such as email spoofing and spamming. Corporate email spoofing involves sending emails that appear to be from a legitimate source but are actually from an attacker. This method is used to trick recipients into divulging sensitive information, […]
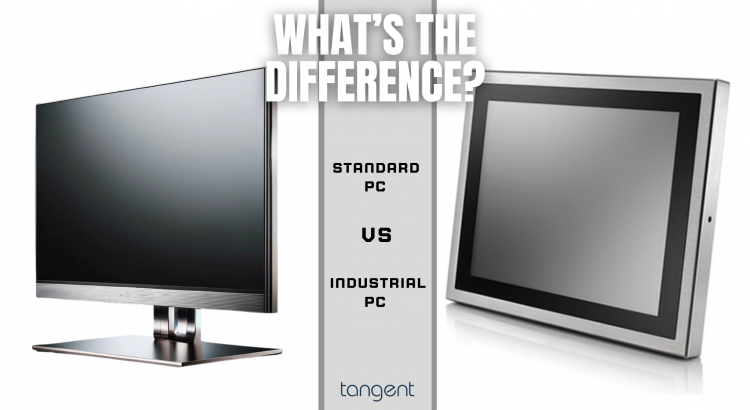
What is the Difference between Industrial PC and a Normal PC?
Industrial PCs vs. Standard PCs: A Detailed Comparison Industrial PCs and normal PCs can be compared to racecars and standard cars. While both are vehicles designed for transportation, one is highly specialized and purpose-built for high-performance on the speedway. Similarly, both industrial PCs and normal PCs are computers, but they serve very different purposes. Normal […]
How Can I Check DMARC?
Use Our DMARC Record Checker Tool to swiftly verify your DMARC records To implement DMARC, you must have a valid DMARC record. To check your DMARC record, you only need to enter your email: Check here. DMARC Director’s Record Check tool will retrieve your DMARC record from the DNS and notify you if no record […]
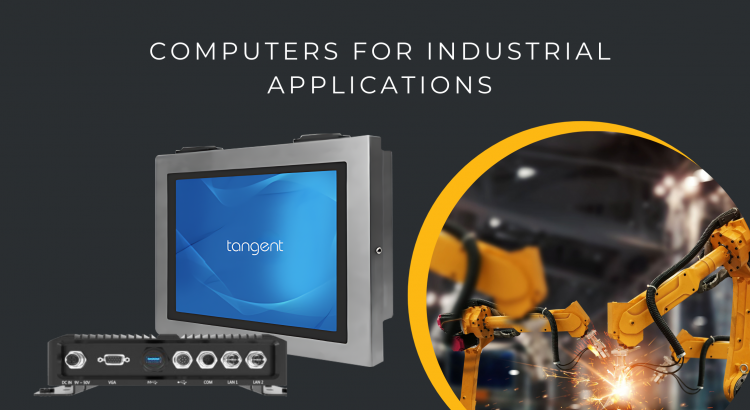
Which Type of Computer is Used in Industry?
Industrial Computers: Essential Solutions for Robust Applications The growing demand for robust computing solutions in various sectors has led to a significant reliance on industrial computers. These specialized systems are engineered for environments where typical consumer-grade PCs would falter. Industries ranging from manufacturing to construction find industrial computers indispensable due to their ability to withstand […]
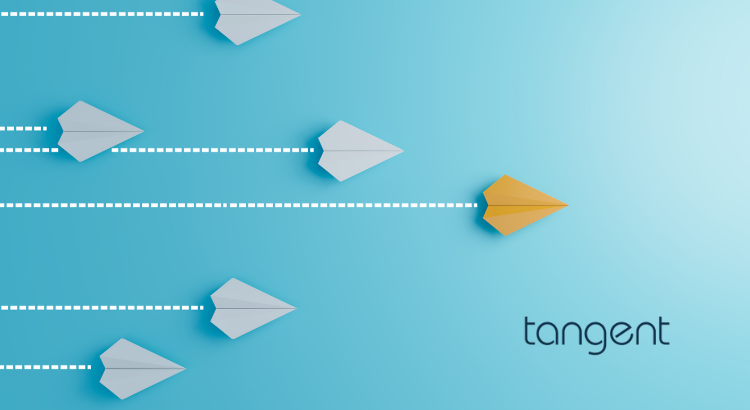
Why a Tangent Partnership Is Your Next Best Move
In today’s fast-paced business environment, staying ahead of the curve isn’t just an advantage; it’s a necessity. At Tangent, we’ve been rigorously analyzing industry trends and the strategies behind most successful businesses. Our deep dive into the mechanics of success has allowed us to pinpoint exactly how we can elevate your business, not just to […]